Indigo dyeing has long captivated cultures worldwide with its deep, iconic blue hues and rich historical significance. To truly master the art of making indigo dye, it's essential to dive into both traditional practices and contemporary innovations. This comprehensive guide brings to light every critical component, ensuring both unparalleled expertise and time-honored credibility in the indigo dye-making craft.
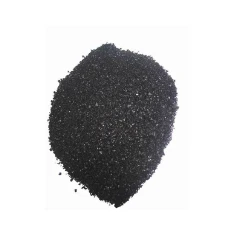
At its core, indigo dyeing involves an intricate, natural process utilizing the leaves of the indigo plant. These plants, belonging to the genus Indigofera, thrive in varied climates from tropical to temperate zones. The pigment extracted from these plants has been used for millennia, valued for its vibrant and lasting color. The process begins with harvesting the indigo plant leaves at their peak, usually before flowering, which ensures the highest concentration of dye precursors.
Once harvested, the leaves undergo fermentation, a pivotal step in traditional indigo dye production. This step involves placing the leaves in a vat of water, allowing natural microbial activity to break down the leaf matter and release indican, the precursor to indigo. The resulting liquid, originally yellowish, is then oxygenated, transforming it into a striking blue pigment. From experience, the art of fermentation is a practice requiring patience and precision. Skilled artisans monitor pH levels, fermentation duration, and environmental conditions to achieve optimal results.
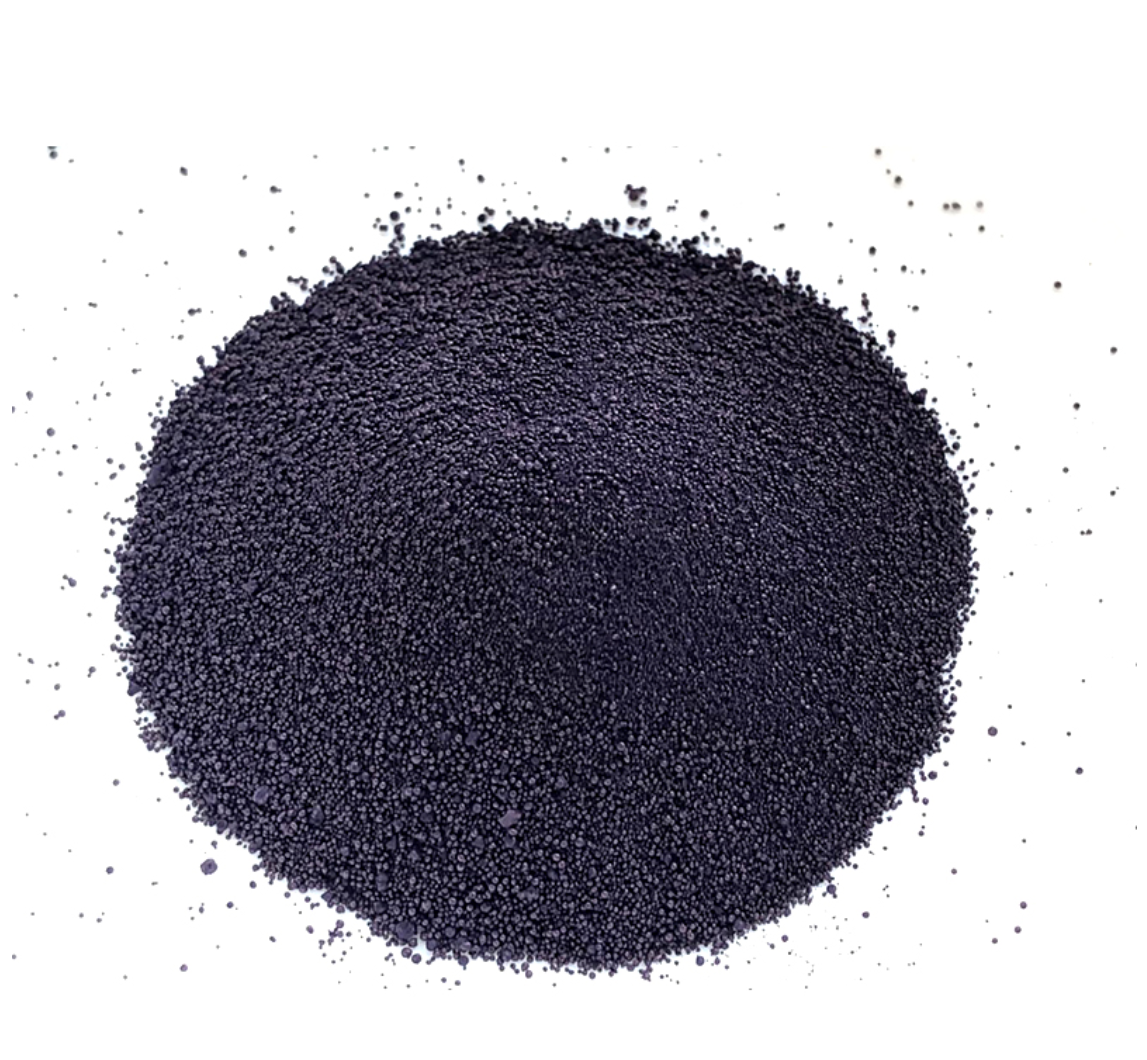
Unlike synthetic dyes, natural indigo dyeing encompasses a unique specificity rooted in tradition. Modern expertise involves marrying these ancient techniques with controlled, scalable processes suitable for contemporary applications. High-quality yields necessitate specialized knowledge in botany, chemistry, and even agricultural best practices, providing not just pigment but a sustainable and eco-friendly dyeing option. This aspect appeals to ethically-minded consumers and brands focused on sustainable fashion and craft.
making indigo dye
For those journeying into commercial production or artisan crafting, the dyeing technique itself requires proficiency. The dyeing process begins with reducing the indigo dye - shifting it from insoluble indigo to a soluble form called leuco-indigo. This conversion allows fabric fibers to accept the dye. Professionals use a vat filled with a reducing agent such as fructose or thiourea dioxide to initiate this transformation. This step ensures a deep bond between the indigo and textiles, resulting in the iconic fade-resistant color.
Indigo's popularity has prompted exploration into varied techniques that extend beyond traditional fabric dyeing into applications including pottery glazing, leather crafting, and even yoga mat coloring. As an authoritative voice in these sectors, expertise about fiber types, mordant use, and creative application methods expands the indigo repertoire. Understanding specific fiber reactions to indigo, such as cotton's absorption versus wool's texture retention, enables custom, premium quality products.
Trustworthiness in indigo dye production is not only about technique but also sustainable practices.
Working directly with indigo cultivators ensures ethical sourcing and community support. Certification standards like GOTS (Global Organic Textile Standard) further authenticate the quality and sustainability of the end product, crucial for consumers who prioritize transparency.
When all these elements converge, the mastery of indigo dye becomes more than just knowledge of craft; it forms an unbroken lineage of cultural heritage infused with modern innovation. By upholding these practices and continually sharing expert knowledge, the indigo dye industry remains vibrant, poised for new discoveries and boundless creativity.