Indigo dye has been revered for centuries, transforming textiles with its rich, deep blue hue. Its journey from ancient civilizations to modern-day fashion reflects not only its enduring appeal but also its versatility in fabric dyeing. This guide delves into the timeless art of using indigo dye for fabric, offering insights drawn from professional experience and expertise.
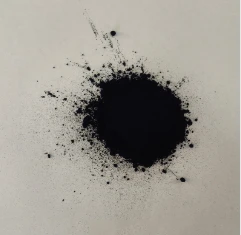
Indigo is derived from the leaves of the indigo plant, primarily found in India, which has been the epicenter of indigo trade for centuries. Unlike synthetic dyes, natural indigo involves a unique fermentation process that transforms indican into the vibrant indigo. This process is pivotal in achieving the dye’s characteristic depth and wash-fast robustness, factors that underline the craft's authenticity.
The experience of working with indigo dye transcends merely applying color; it’s an immersion into a historical craft. One must understand the intricate chemistry involved. Typically, indigo dyeing involves a reduction vat process, turning insoluble indigo into a soluble form, which penetrates the fabric easily. The fabric changes from green to blue as it oxidizes upon removal from the vat—a magical transformation that is as thrilling to the first-time designer as it is to a seasoned artisan.
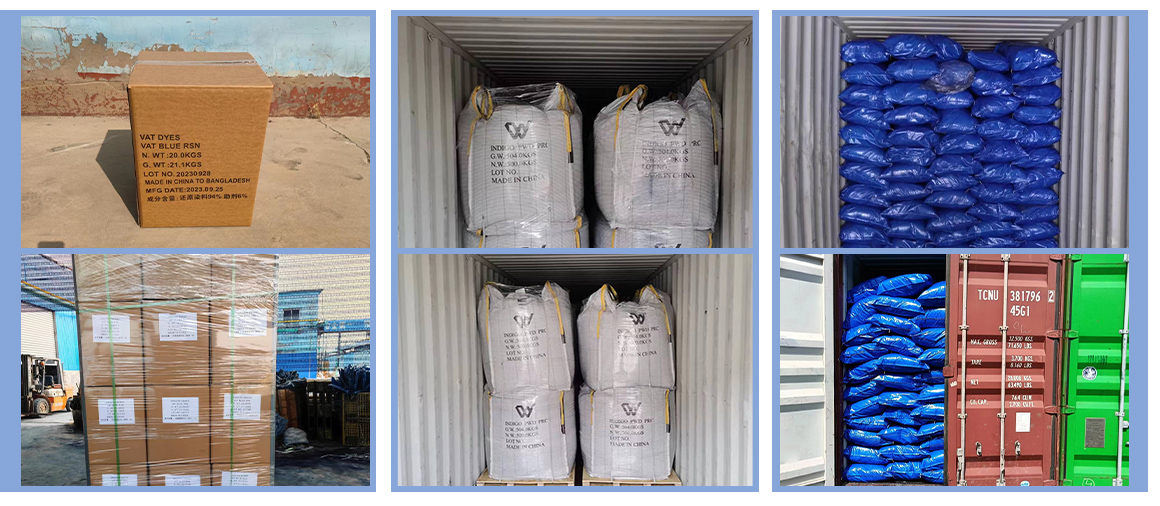
Professionals in the field often emphasize the trial and error aspect that accompanies working with indigo. This dye has an enigmatic quality it requires careful attention to detail. Variables such as the type of fabric, its pre-treatment, the concentration of the dye bath, and even the climatic conditions during dyeing can influence the final color outcome. Cotton, linen, and wool are exemplary candidates for indigo dyeing, as their fibers respond well to the dye’s properties. Synthetic fabrics, however, may require additional treatments to achieve the same level of vibrancy.
indigo dye for fabric
From an expertise standpoint, ensuring color fastness and uniformity is critical. Pre-washing the fabric to remove any residues and using mordants can enhance dye uptake and retention. Techniques such as shibori or tie-dye, which create patterns through folding, twisting, or bunching fabric, showcase indigo’s versatility. These methods allow artisans to unlock a myriad of designs, each unique and unreplicable. True expertise is demonstrated by those who can harness indigo’s complexities, achieving consistent and desirable results batch after batch.
In terms of authoritativeness, the sustainability of natural indigo dyeing cannot be overlooked. The resurgence of eco-friendly fashion has amplified indigo’s prominence, setting it apart from environmentally harmful synthetic dyes. This renaissance is not just a commercial trend but a recognition of the dye’s minimal ecological footprint. Engaging with indigo dyeing supports sustainable practices and empowers artisanal communities, particularly in regions where indigo has cultural significance.
Building trustworthiness involves acknowledging indigo’s challenges and working within its limitations. Transparent communication about the possibilities and constraints of indigo dye with clients and consumers builds credibility. Customers who appreciate handmade pieces value the narrative of creation, understanding that variations in color and pattern are not flaws but rather signatures of authenticity.
In summation, indigo dye's art and science provide a dual path of exploration for those interested in fabric alteration. It is a medium that offers a blend of tradition and innovation, where heritage techniques meet contemporary applications. For designers, crafters, and consumers alike, engaging with indigo dye is about more than color; it's about embracing a legacy that intertwines history with modern sustainability, an embodiment of artistry and eco-consciousness.