The Art of Setting Indigo Dye A Journey into the Best Practices
The process of setting indigo dye, a color so deeply rooted in the history and culture of various civilizations, is both an art and a science. Indigo, renowned for its deep blue hue, has captivated the hearts of textile artisans and fashion enthusiasts alike. To achieve the best setting, one must delve into the alchemy of this ancient dye, understanding its complex relationship with fabric and the environment.
Indigo dyeing is not merely a matter of submerging cloth into a vat filled with dye; it's about controlling the intricate chemical reactions that lead to the desired shade. The key to achieving a lasting, vibrant indigo hue lies in the reduction process. Indigo vat requires a reducing agent, traditionally fructose or glucose from materials like molasses, to activate the dye's pigment. This step is crucial because indigo, in its natural state, is insoluble in water and must be converted into a soluble form known as leuco-indigo to penetrate the fibers.
Temperature control is another critical factor. The ideal temperature range for indigo dyeing is between 50-60°C (122-140°F). At this temperature, the dye molecules move rapidly, enhancing their absorption into the fibers. However, exceeding this threshold can cause the dye to decompose, resulting in uneven coloration or loss of intensity.
The type of fabric also plays a significant role
The type of fabric also plays a significant role
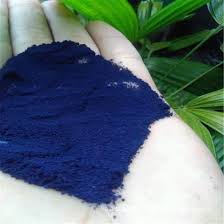
The type of fabric also plays a significant role
The type of fabric also plays a significant role
best setting indigo dye. Natural fibers such as cotton, linen, and hemp are ideal for indigo dyeing due to their porosity and ability to form strong hydrogen bonds with the dye. These bonds ensure the color's longevity, allowing the fabric to weather countless wash cycles without losing its vibrancy.
The technique of applying the dye, whether it be through dip-dyeing, brushing, or printing, further refines the outcome. Each method offers unique aesthetic qualities and levels of control over the final appearance. Dip-dyeing, for instance, yields a gradient effect, while brushing allows for precise pattern creation.
Finally, the setting process is completed by airing the dyed fabric, enabling oxidation to take place. This step is where the magic happens – the indigo transforms from its reduced state back to its original insoluble form, locking the color permanently into the fibers.
In conclusion, the best setting of indigo dye involves a harmonious blend of art and science. It demands an understanding of chemical processes, meticulous control over variables like temperature and material choice, and a touch of creativity in application. By mastering these elements, one can achieve a fabric that is not only visually stunning but also a testament to the timeless allure of indigo dye.