Indigo dye has been a popular choice for fabric dyeing for centuries, known for its vibrant blue color and long-lasting properties. Setting indigo dye in fabric is a crucial step in the dyeing process to ensure that the color remains vibrant and does not bleed or fade easily. Fabric companies that specialize in indigo dyeing must pay close attention to this important step to produce high-quality fabrics that meet customer expectations.
Setting indigo dye in fabric involves fixing the dye onto the fibers of the fabric through a variety of methods. One common method is to use a reducing agent, such as sodium hydrosulfite, to help the dye penetrate the fibers and bind to them more effectively. This step is often done in a bath of hot water or steam to help the dye fully saturate the fabric. After the fabric is dyed, it is rinsed thoroughly to remove any excess dye and then dried or cured to set the color.
Achieving the right shade of blue and ensuring that the color remains stable over time are essential considerations when setting indigo dye in fabric. Fabric companies must carefully monitor the dyeing process, including water temperature, dye concentration, and immersion time, to achieve consistent results. Quality control measures are also important to ensure that each batch of fabric meets the company's standards for color fastness and durability.
In addition to traditional methods of setting indigo dye, some fabric companies may use innovative techniques to enhance the color and performance of the fabric
In addition to traditional methods of setting indigo dye, some fabric companies may use innovative techniques to enhance the color and performance of the fabric
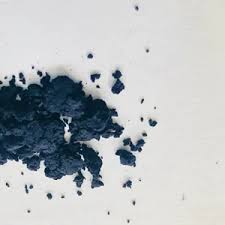
In addition to traditional methods of setting indigo dye, some fabric companies may use innovative techniques to enhance the color and performance of the fabric
In addition to traditional methods of setting indigo dye, some fabric companies may use innovative techniques to enhance the color and performance of the fabric
setting indigo dye in fabric company. For example, some companies may use special binders or fixatives to help the dye adhere to the fabric more effectively and resist fading. Others may use advanced machinery and technology to automate the dyeing process and improve efficiency.
Consumers who purchase indigo-dyed fabrics expect them to be colorfast and durable, able to withstand repeated washings and wear. By properly setting the dye in the fabric, fabric companies can meet these expectations and produce high-quality products that are in demand in the market. Whether it's denim for jeans, upholstery fabric for furniture, or clothing for fashion, indigo-dyed fabrics have a timeless appeal and a wide range of applications.
In conclusion, setting indigo dye in fabric is a critical step in the dyeing process that requires precision and care. Fabric companies that specialize in indigo dyeing must have a deep understanding of the dyeing process and a commitment to quality to produce fabrics that meet customer expectations. By investing in the right equipment, techniques, and expertise, these companies can create indigo-dyed fabrics that are vibrant, long-lasting, and in-demand in the market.