Indigo Dye An OEM's Journey to Perfection
The process of making indigo dye, a traditional natural colorant extracted from the leaves of plants belonging to the Indigofera and Isatis species, is an intricate art form that demands precision, patience, and passion. For original equipment manufacturers (OEMs) specializing in textiles and fabrics, mastering the art of indigo dye production is not just a commercial endeavor but a quest for authenticity and quality.
The journey begins with the selection of premium plant material, which serves as the raw source for the dye. Harvest time is crucial; young leaves yield the most vibrant colors, while older leaves produce more muted shades. Once collected, the leaves undergo a fermentation process that can take several days, depending on the desired hue and intensity. This step is pivotal as it converts the glycoside present in the leaves into indoxyl, the precursor of indigo.
Next, the fermented leaves are transferred to a vat filled with water, where they are beaten or stirred vigorously to release the dye. The liquid is then allowed to settle, forming layers of sediment and clearer water above. The magic happens at this juncture when oxygen in the air reacts with the indoxyl, resulting in a bright blue pigment rising to the surface.
For OEMs, consistency is key. They must ensure that each batch of dye matches the previous one in terms of shade and longevity. To achieve this, they employ strict quality control measures, from monitoring the pH levels of the vat to controlling the temperature and duration of dyeing To achieve this, they employ strict quality control measures, from monitoring the pH levels of the vat to controlling the temperature and duration of dyeing
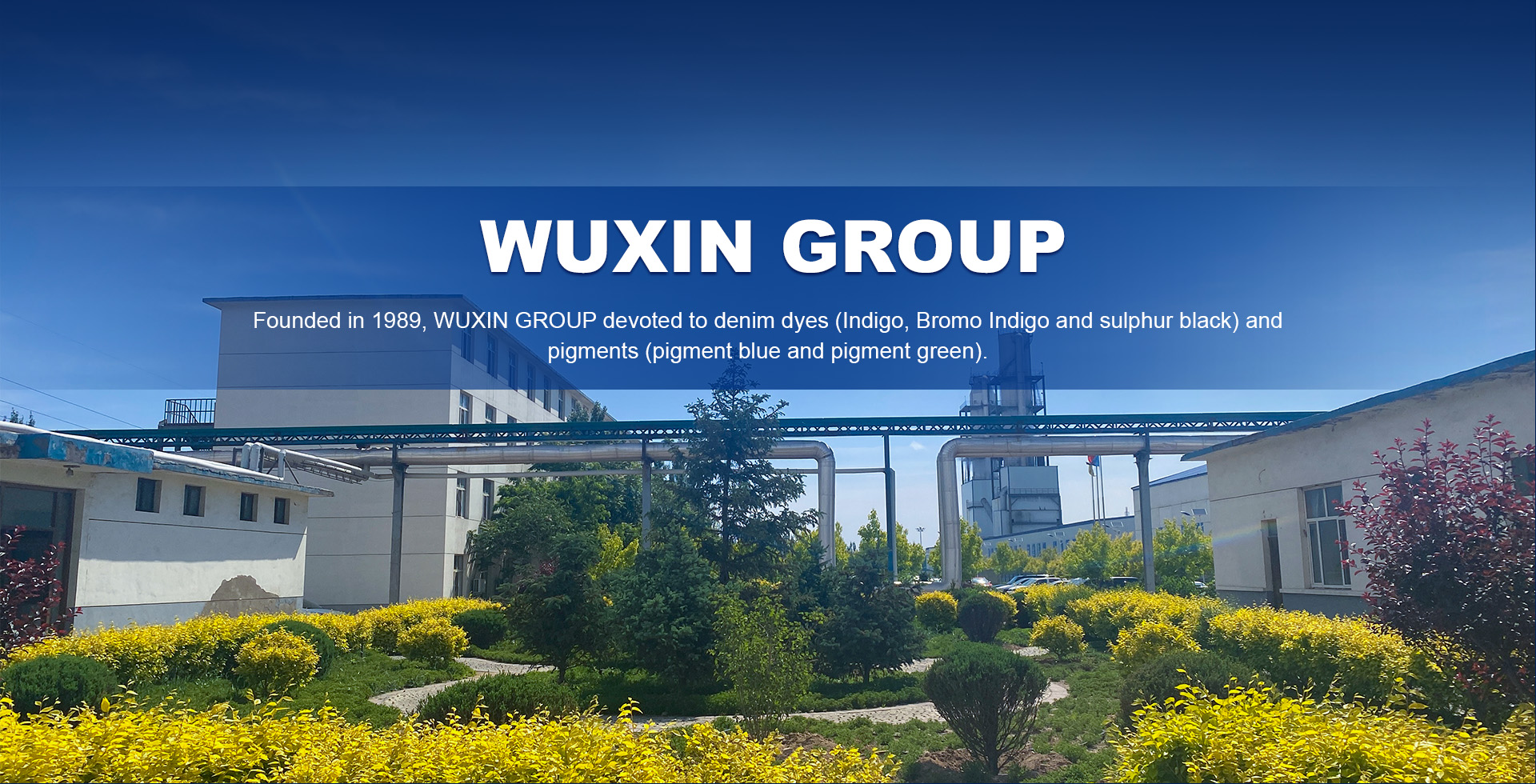
To achieve this, they employ strict quality control measures, from monitoring the pH levels of the vat to controlling the temperature and duration of dyeing To achieve this, they employ strict quality control measures, from monitoring the pH levels of the vat to controlling the temperature and duration of dyeing
oem making indigo dye. Moreover, they often integrate modern techniques such as digital color analysis to fine-tune the process further.
In addition to technical prowess, OEMs also need to consider environmental impacts. The traditional indigo dyeing process, while beautiful, can be harmful if chemicals and waste are not managed properly. Thus, many forward-thinking manufacturers have turned to organic farming practices for their plant sources and implemented water recycling systems to minimize ecological footprints.
The end products—fabrics colored with indigo dye—are not only aesthetically pleasing but also carry stories of tradition, innovation, and sustainability. Consumers worldwide seek out these unique pieces, appreciating the depth of history and craftsmanship behind each garment.
In conclusion, the OEM's journey in making indigo dye reflects a blend of science and artistry, technology and tradition. It represents a commitment to preserving ancient techniques while embracing modern advancements to cater to global demands for high-quality, eco-friendly textiles. As this journey continues, so too does the fascination with indigo—a living testament to human creativity and our enduring connection to the natural world.